Flexographic printing machine are popular for their flexibility, efficiency and environmental friendliness, but choosing a "tailor-made" flexographic printing machine is not easy. This requires comprehensive consideration of material properties, printing technology, equipment performance and production needs. From plastic film to metal foil, from food packaging paper to medical labels, each material has unique characteristics, and the mission of the flexographic printing machine is to tame these differences with technology and achieve the perfect expression of color and texture in high-speed operation.
Taking common plastic films as an example, materials such as PE and PP are light, soft and easy to stretch, requiring highly sensitive tension control to prevent stretching deformation. If the tension control system of the flexographic printing machine is not sensitive enough, the material may deform or even break during high-speed transmission. At this time, a plastic flexo printing machine equipped with servo drive and closed-loop tension control becomes a rigid demand. When facing paper or cardboard, the challenge turns to ink absorption and environmental stability. This type of material is extremely sensitive to humidity, prone to shrinkage and curling under wet conditions, and may crack after drying. At this time, the paper flexo printing press not only needs to be equipped with an efficient hot air drying system, but also needs to add a humidity balance module in the paper feeding path, just like weaving an invisible protective net for the paper. If the printing object is metal foil or composite material, the machine is required to have stronger pressure regulation ability to ensure the adhesion of ink on non-absorbent surface. In addition, if it involves food and pharmaceutical packaging, it is also necessary to choose a model that supports food-grade ink and UV curing system to meet safety standards.
In short, from material properties, process goals to production rhythm, the needs are locked layer by layer, making the equipment a "custom tailor" of the material, choosing to find the optimal solution between material limits, process accuracy and cost efficiency. A flexo printing machine that "understands materials" is not only a tool, but also a key to crossing the market threshold.
● Printing Samples
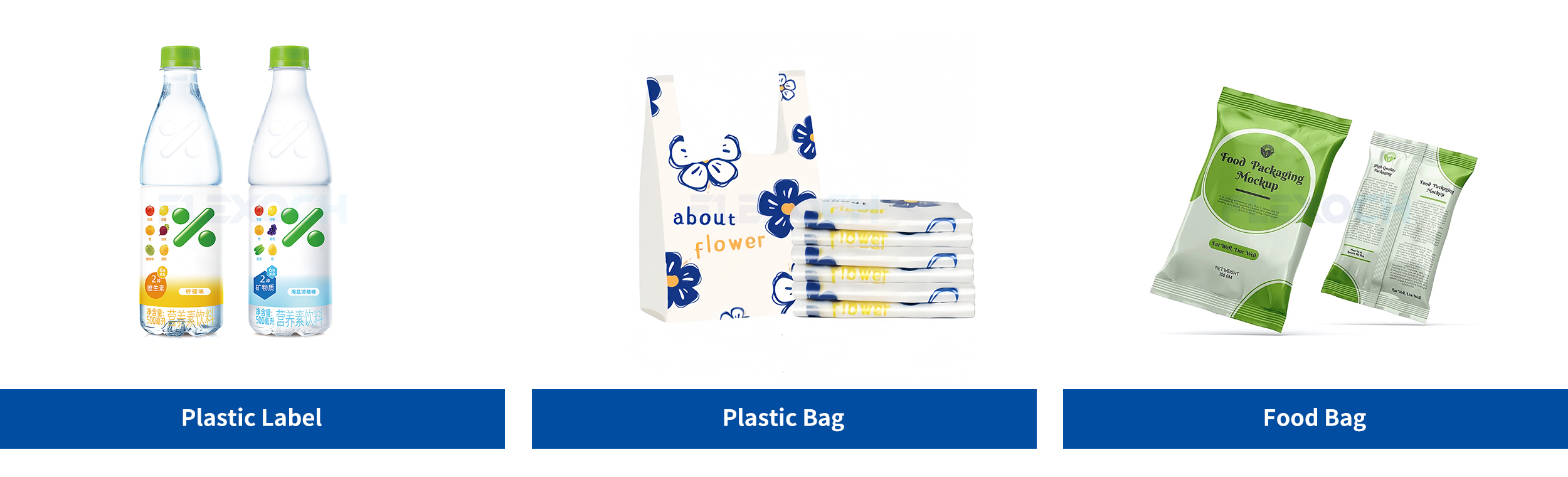
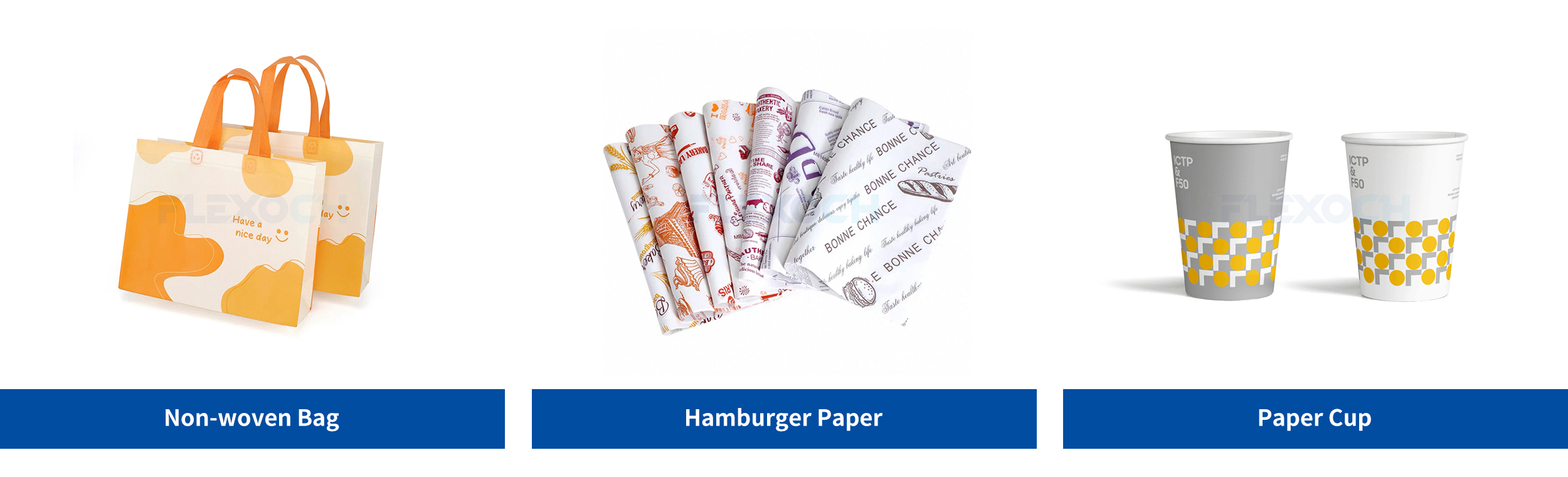
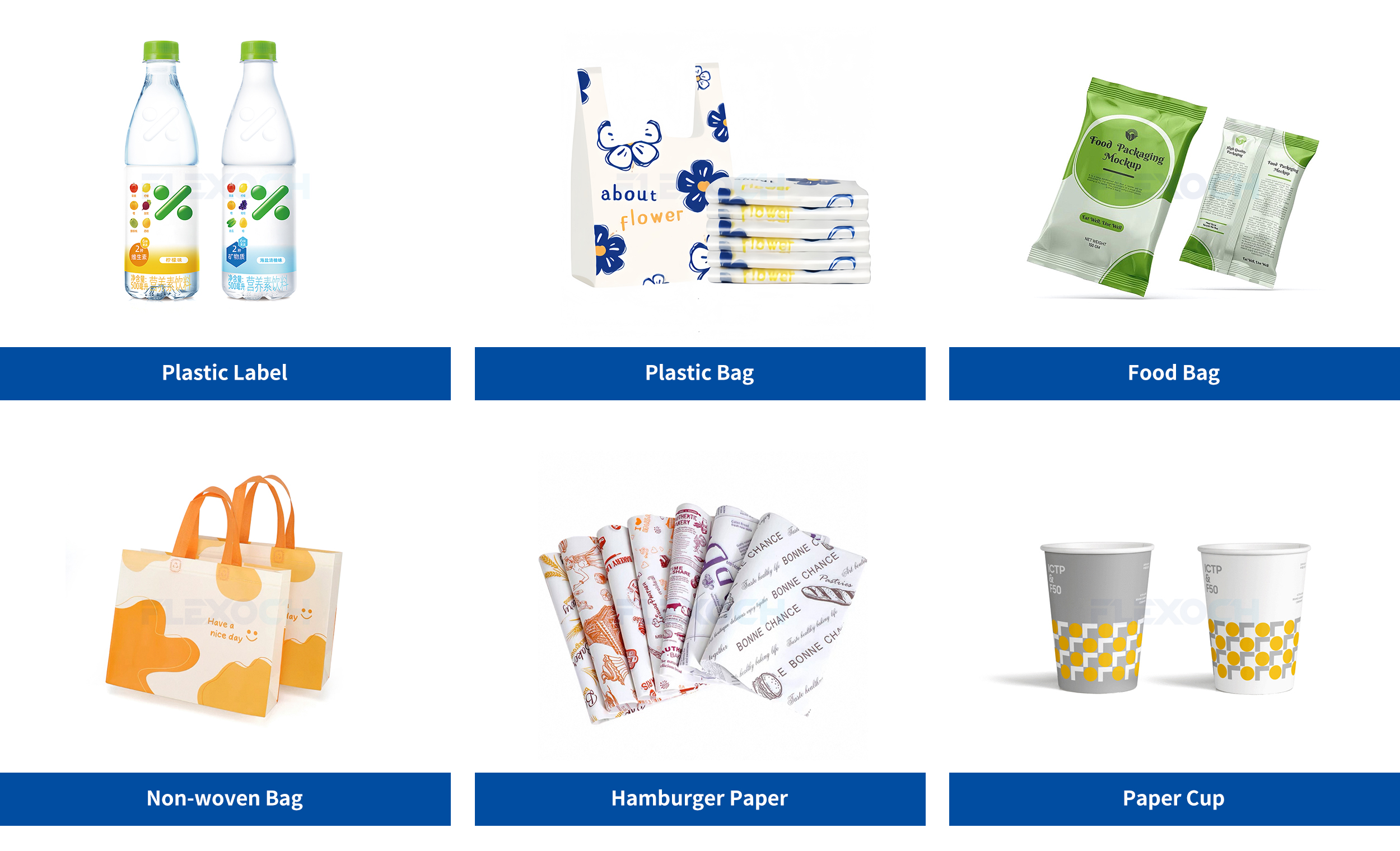
Post time: Apr-12-2025